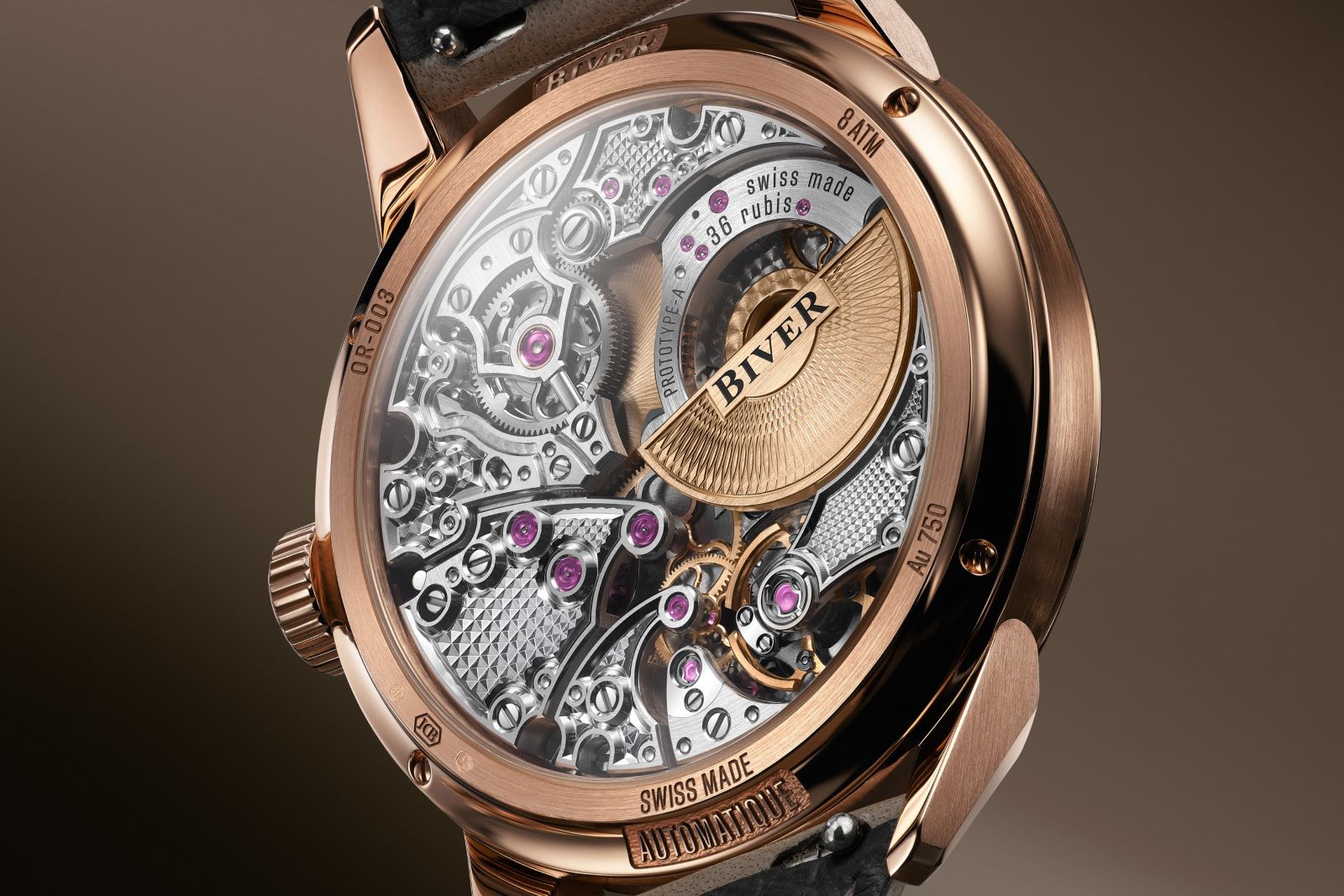
We recently looked at the amazing artisanal finishing techniques. But what if you were to flip over a watch and look through the exhibition caseback? What are some of the most common and important types of finishing found on the beating heart of a watch? Between striping, perlage and brushing, these are some of the quintessential movement finishing techniques every collector should be able to identify.
Anglage


Also known by the French term bevelling or chamfering, this finishing technique sets the standard for haute horology movements. If you look at the flank of a movement bridge, if there is a 45-degree angled, polished bevel that catches the light, this is the perfect example. This bevelled detail is one of the most complex and time-consuming techniques, and from a technical standpoint, believed to prevent material stress concentrations along the edges of bridgework.
A decorator will carefully smooth down edges with files and sometimes a micro-rotor tool with an ebony tip to form a uniform width and two sharp parallel lines. The surface of the sloping angle is then hand-finished with files and wood pegs with abrasive paste, giving a polish that is incomparable to machine-made attempts. It is a time-consuming technique that requires years of experience and a patient hand and is seen as the recognisable feature of a top tier watch movement. The pièce de resistance is curved outer bevelling, as rounded angles can only be done by hand without the possibility of going straight from point to point. Here, the surface of the chamfer is also convex, and only a few extremely trained hands can achieve this after many years of training.
Biver Automatique
We’ve already reviewed this magnificent beast of a watch (the rose gold version specifically), so for the full rundown head to our review section. But in brief, every part of the watch is finished to perfection and that includes bevelling on every single edge of the movement. It’s magnificent and shows off a lot of the techniques listed here, but it’s the way the light hits the anglage that really sets it off.
Striping
Also known as Côtes de Genève, Côtes de Glashütte or Côtes de Fleurier depending on the exact regional variation, striping is the wave-like linear pattern on movement bridges, 3⁄4 plates and often rotors. It is an instantly recognisable mechanical movement feature and perhaps the most recognisable metal finishing method together with perlage. As with many forms of metal finishing, it had a functional purpose that, with today’s precision and sealing technology, is almost rendered obsolete. The interesting and undulating surface was originally intended to keep dust and particles away from the gears and other smaller components of the movement, and it still works to do so.
With today’s strict quality control within an atelier and improved seals for watch cases, it has become a decorative part of a movement. The stripes are machine-applied in a symmetric, straight or circular pattern and must be perfectly aligned on adjoining pieces of bridgework.
Daniel Roth Extra Plat
Sure, there are a lot of different finishes you could use the latest from Daniel Roth to illustrate. But along with everything happening on the dial, it has some of the cleanest, most beautiful striping on the movement of any watch. With its large plates uninterrupted by a rotor – it’s manual-wind, of course – the striping has room to show off and it makes the most of it. This is exactly what you’d expect from the revival of an iconoclastic independent watchmaker.
Perlage
Perlage and perlée are French words used for a pearl-like pattern often used inside watch cases or the mainplate. Since its infancy, the automotive industry has used large-scale perlée patterns on surfaces such as car dashboards. These days, that parallel is confined to luxury vehicles like Paganis and the Bugatti Veyron 16.4, echoing the perlage of vintage Bugatti single seaters. This light-catching and decorative pattern offers intricate overlapping circles that can be machined – or hand-made. It is mostly used to finish larger surfaces that are not in your line of sight.
The size of the small circles and their concentric accuracy is a tell-tale sign of top-tier watchmaking. When done by hand, perlage needs the rock-steady hand of a trained artisan who uses a rotating abrasive tip or peg pressed onto the metal in overlapping patterns of circles. The difficulty lies in achieving a consistent pattern across a larger piece of metal. Still, as with all finishings, a few tell-tale microscopic flaws only underline the charm of the craft.
Piaget Polo Flying Tourbillon
Perlage is a relatively common sight through an open caseback, especially at a certain echelon of watchmaking, but through the dial is another matter. Piaget’s first ever Polo- mounted flying tourbillon opens up the front of the dial just enough to show some of those precise circles underneath the handset. With finishing like this, who even needs a dial?
Black Polish
Any metal polishing technique which aims to achieve a smooth gloss surface that will reflect light, to elevate the appearance of a part while ensuring fit and quality. The enigmatic technique of black polish, also known as miroir or poli noir in French (mirror, in English), is a term that conjures up images of horological alchemy and is the food of legends. Or if you’re talking about Grand Seiko, the term Zaratsu polishing refers to the same concept.
The resulting finish is a mirror-like polish that appears pure black at an acute angle, hence the name. After preparing the component’s metal and ensuring no surface irregularities are present, it will be polished face down on a zinc plate, onto which an abrasive diamond paste is added. Using a careful circular motion, it is a detailed and minute process that takes a steady hand, gradually using finer pastes in stages to achieve a mirror-flattened surface.
Grand Seiko Evolution 9 Spring Drive U.F.A Ice Forest
Black or Zaratsu polish is typically a technique most commonly used on a watch’s case but it can be seen on movements as well. The Grand Seiko Evolution 9 Spring Drive U.F.A Ice Forest uses it on the bevelled edges of the 9RB2. It’s actually an example of a watch brand combining multiple finishing techniques, using the polish to highlight the elements of anglage.
Satin Brush
Satin brushing is one of the most common types of finishing in all of watchmaking, not just in movements. It’s technically a type of polish but uses an abrasive pad in order to mark the metal with lines parallel to the direction of polishing. It’s popular due to its relative ease of application while also creating a good looking effect that makes the use of metal’s natural lustre and shine.
There are multiple styles of brushed finishing that can be applied to a movement’s components. A plate or bridge might have a unidirectional brush to it with all the grain of the brushed lines oriented in the same direction. Alternatives include circular grained brushing, where the lines arc along a curve, such as following the curve of a rotor. Another popular one is sunray brushing, where the lines radiate outward from a central point, typically used on circular components such as the barrel cover (or more commonly a watch’s dial).
IWC Ingenieur Perpetual Calendar
Released during Watches & Wonders, the IWC Ingenieur Perpetual Calendar introduces the first haute horology complication to the revived integrated bracelet sports watch collection. A brushed finish on the calibre IWC 82600 makes a lot of sense. It adds a nice sense of refinement without going over the top with ostentatious engraving, leaning into the industrial, utilitarian influences behind the watch’s design.
Engraving
There are huge number of engraving techniques that can be used across a watch, including on the movement. We covered lots of specific styles such as guilloché or hand-engraving in our article on artisanal dial finishes and all the information there applies to movements too. The main distinction when it comes to a movement is that you’ll more often see engraved lettering. Whether that’s the brand’s logo on a rotor or details about the movement itself such as number of jewels or a reference number. Or potentially the Poinçon de Genève – a special seal of approval that you can read all about in Oracle Time Issue 111.
A.Lange & Söhne 1815
The A. Lange & Söhne 1815 34mm released at Watches & Wonders features multiple styles of engraving. At the simplest level it features engravings of the brand’s name and details. But also, connecting to the balance wheel the main bridge on display is decoration with a curling and furling floral motif.
Oracle Time